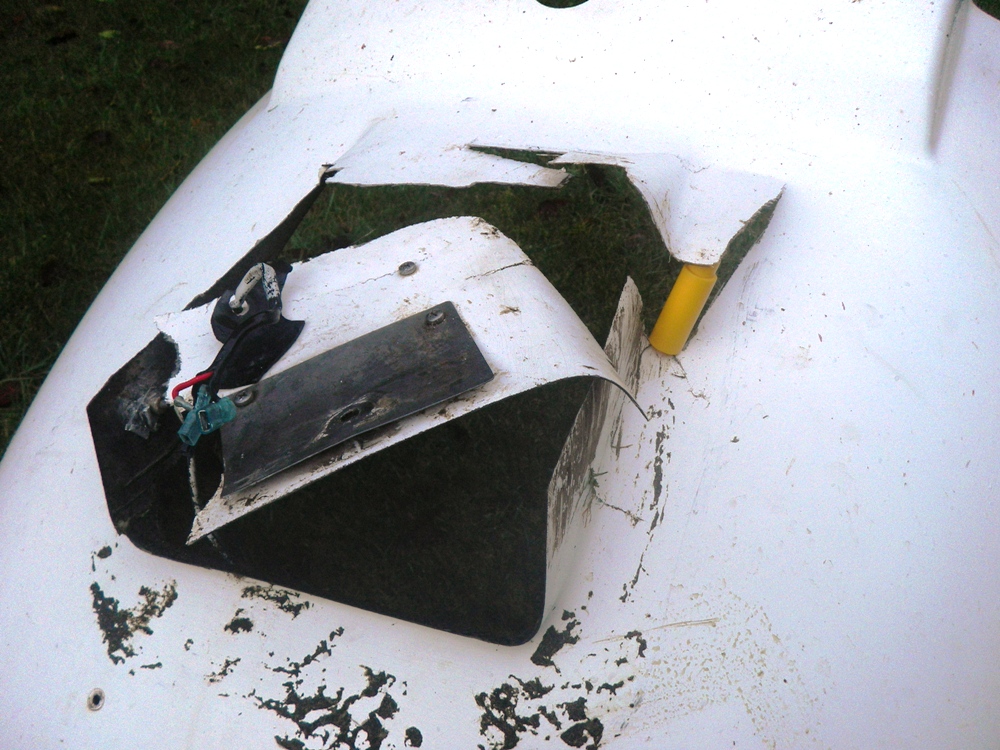
“Can you fix it?” was his question. The air intake was obviously smashed. Fortunately, he had all the broken pieces, so I’d be able to re-create the original shape.
The related stress cracks were relatively easy to trace and no problem to fix.
In addition, the exhaust pipes and muffler had been rubbing on the cowling. We found charred carbon laminate under the ‘heat proof’ shields. So more clearance between hot metal and cowling was required.
“Of course I can,” I replied after quickly running thru the possible repair scenarios in my mind. I was very conscious of the need to do a professional repair restoring strength and flexibility, but with no weight increase. “And fix the exhaust problems at the same time.”
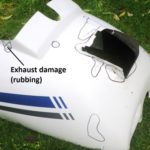
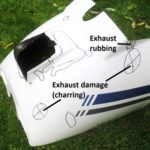
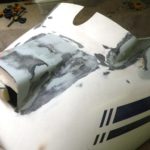
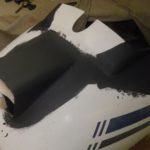
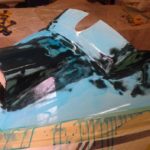
First task was to carefully re-create the missing air intake shape from all the broken pieces. A bit like gluing a broken eggshell together. Humpty Dumpty all over again.
To increase the air gap near hot exhaust parts, the air outlet was widened and a strategic ‘bulge’ was added.
This new cowling shape was filled, faired, surface primed, spot-filled, pinhole-filled, etc to get the shape correct and the surface smooth. Then waxed and sprayed with release agent.
At this stage, I made a temporary fibreglass part-mould of the lower cowling.
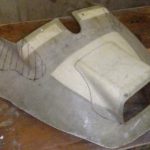
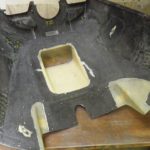
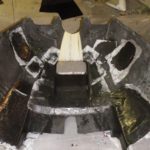
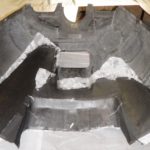
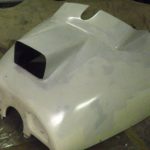
The lower cowling was cut back and prepped, before the part-mould was mated with it.
I laid-up carbon fabric to create a new air intake, wider air outlet and an exhaust ‘bulge’. Final job was to fill and prime the outside ready for painting.
The rebuilt cowling is as strong and lightweight as the original, but with better exhaust clearance. I even incorporated a sturdier landing light mount.