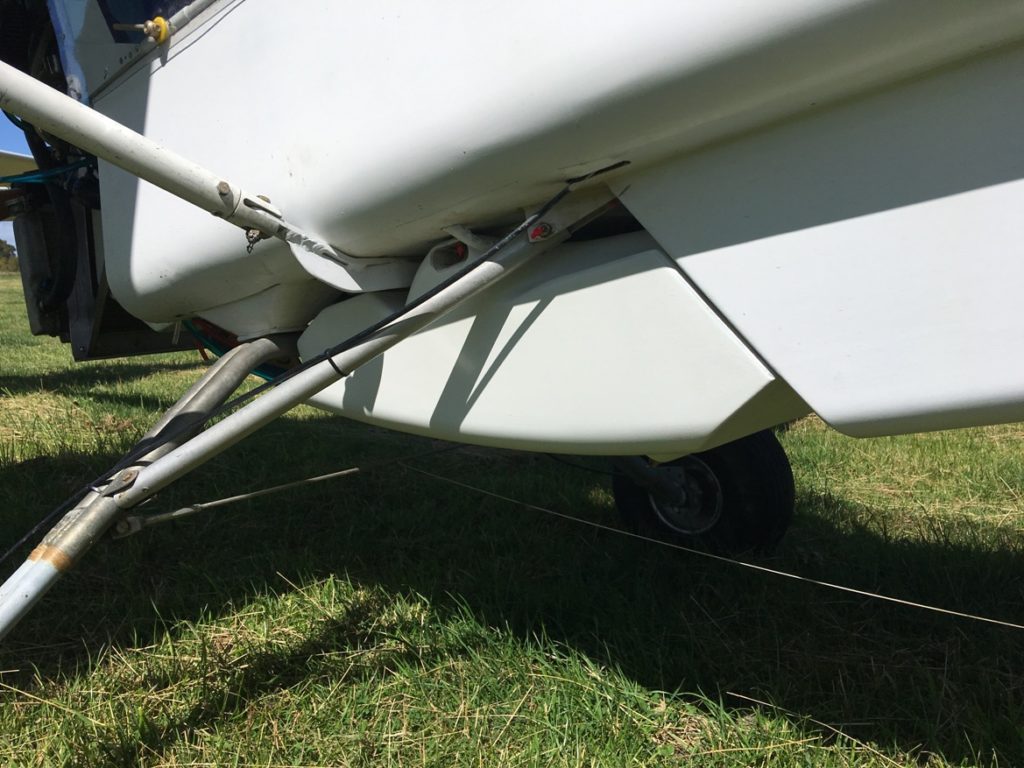
The original fuel tank on the Shadow microlight is only 23 litres. That’s very small when you’ve got a thirsty 2-stroke. I’ve done some one-hour flights, but you can’t afford to ‘linger’ en-route.
Many Shadow and Streak owners fit an underbelly ‘slipper’ tank to gain extra flying time.
Working part-time in the Fi Innovations composites factory, I have access to some pretty cool technology. I decided to use vacuum-assisted resin infusion to build my slipper tank.
Derakane vinylester (like they make commercial petrol storage tanks from) is the preferred resin, because it does not get attacked by petrol.
After making and sealing an MDF and plywood mould, I carefully laid double-bias fibreglass fabric, stiffened with fuel-resistant foam core and layers of glass tissue inside. Resin inlet and outlet ports were fitted, then everything was sealed inside a see-thru plastic film, I applied a 99% vacuum for 30 minutes.
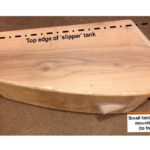
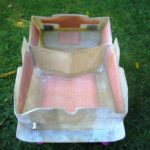
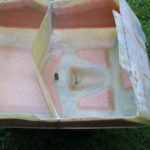
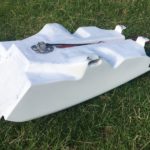
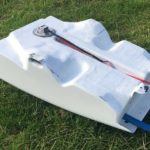
The magic happens when you open the inlet tap. It only takes a few minutes for the vinylester resin to completely saturate the reinforcements. Excess resin is automatically sucked out, so you end up with a lightweight, strong structure.
The tank’s top moulding was complicated. I designed it to fit around the undercarriage braces and wing strut tie-bar.
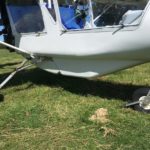
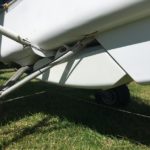
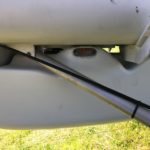
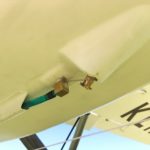
The fuel sender is shrouded by its own cylindrical baffle, so that the fuel gauge reading is unaffected by any surge.
Six mounting points were added, each one strong enough to hold the fuel tank on its own. Probably over-built.
Lots of testing followed for leaks, unusable fuel and fuel feed. Fuel gauge was calibrated. Then it was off into the sky.
Now with 50 litres fuel, I can fly for 2.25 hours or more. Great. If only my bladder would last that long!