The tail boom has been fitted into the centre section and the nose cone has been repaired and trimmed to fit around the footwell fairing. Now its time for painting the fuselage.
Glass, fill, sand, fill, sand . . . . .
Recently, I’ve done hours of fibre-glassing, filling and sanding on the fuselage rear footwell and wing centre section to get them reinforced and smooth for painting. Side windows have been cut out (between the front and rear canopies) to widen the pilot’s field of view. An improved fuel transfer system has been fitted, so by twisting a lever the pilot can quickly transfer fuel from the wing tank down to the main tank. The wiring loom, new brake cables, new elevator trim cable and new elevator Teleflex cable have now been threaded into place, and the kevlar sides have now been glued onto the fuselage.
overhaul pitch/roll control system
Apart from the crash-damaged parts of the Parson gyrocopter, some other linkages of its pitch/roll control system were found to be worn and/or distorted, so they have been overhauled and strengthened. Several new components needed to be machined/fabricated. As a safety precaution, all the control rod ends, bolts and bushes have also been replaced. Bruce was pleased that the progress inspection by a gyro expert went very well. It confirmed his decisions and provisionally approved the work that he had completed.
gyro repairs
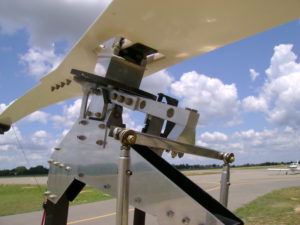
Over 2012-2013, Bruce took on getting a crash-damaged Parsons Tandem gyrocopter from Cromwell airworthy again. It has proved to be an exercise in patience involving such diverse delights as getting the rotor head components crack-tested, sourcing a new Australian AK extruded rotor blades, importing a German overrun bearing (sprag clutch) and various specialist alloy extrusions.
all done
what you find when you start on a job
Some of the unexpected tasks were to un-sieze the rudder fin post from the boom, repair broken ribs inside the fin and to replace the fibreglass around the rear boom support cross-member (which had been cut away to give extra tip clearance for the prop). While it was apart, Bruce had the tailplane mounting tubes crack-tested and did the common Shadow upgrade of fitting UHMWPE bushes inside the boom to prevent further wear on these mounting tubes.
urgent repair
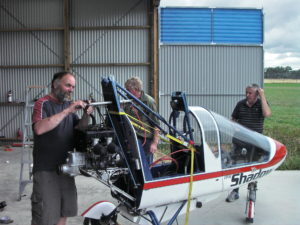
In February 2012, Bruce completed urgent repairs to a Shadow C-D from Wanaka. It had been grounded because of excessive wear in the wing-to-fuselage attachments. The job involved completely removing the boom from the centre section, in order to fit new alloy doublers, bush the ovalised holes and replace the wing attachment bolts. The actual repairs were very quick, with most of the labour absorbed in dismantling, re-assembly, covering and painting.
Mods approved
RAANZ has approved some mods, so Bruce has constructed an up-rated 450kg main undercarriage and added a deeper footwell for passenger comfort (with a streamlined fibreglass fairing). Lots of fun has been had machining undercarriage inserts, axle spacers, threaded inserts (for fitting rod ends) and window latch parts.
Bruce’s Shadow rebuild
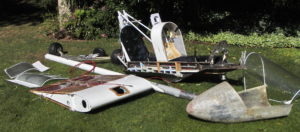
Bruce’s personal project is re-building and modifying ZK-KLH, a Shadow B-D microlight. Murray Hagen originally built this aircraft in 1989, alongside its sister CFM kit plane ZK-TTE. After seven years of flying, dogged by many engine failures, one day the Rotax 532 finally gave up. The result was a ‘less-than-happy’ landing breaking the main landing gear and damaging a wingtip.
During storage one of the big Fiordland earthquakes damaged the wing leading edge, a prop blade was broken and pesky starlings had picked huge amounts of foam out of the centre section ribs. Fortunately Murray was able to supply spare foam, plywood, new wingtips, new main landing gear, a replacement prop (custom built by Brent Thompson) and an unused Rotax 582 engine.
The wing’s 1.2m plywood leading edge has now been repaired. Much of the restoration work on the fuselage and wings has now been completed. The aluminium joining tubes of the tail feathers have been crack-tested – some replacements and reinforcing were neccessary. UHMWPE bushes have been fitted inside the tail boom to stop wear on the tailplane mounting tubes. The tail surfaces have been re-covered with polyester fabric.