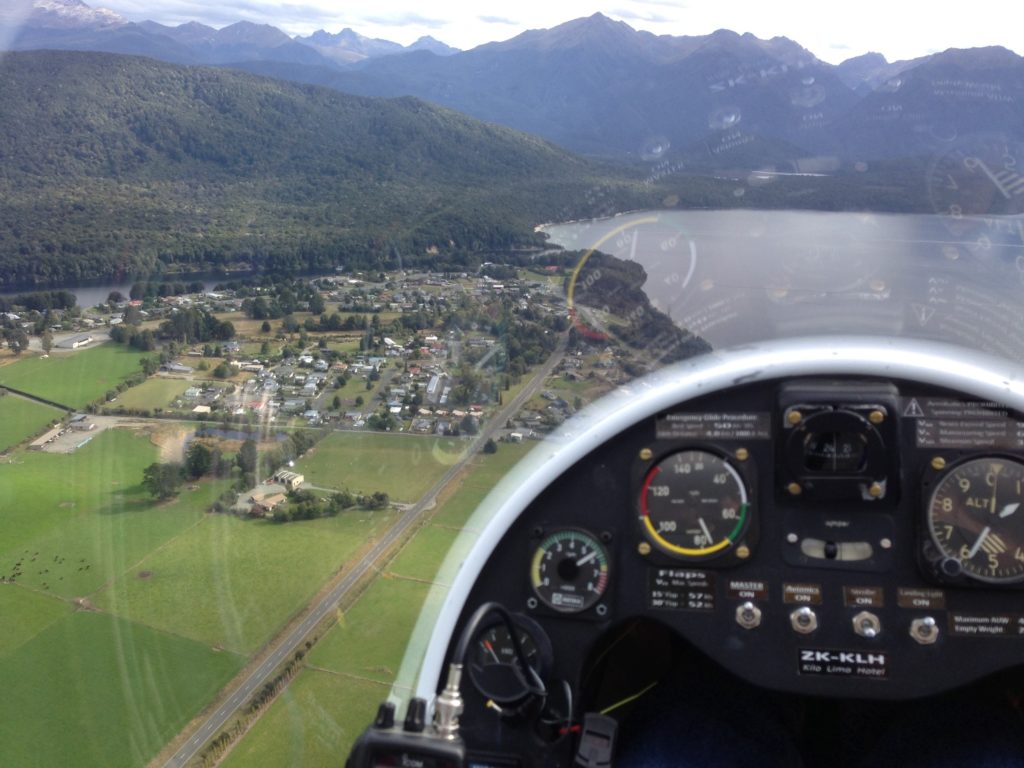
I travelled back up to Manapouri Airport to do some familiarisation in the Shadow microlight. Two days of near calm weather – perfect for me. Under Murray’s supervision, I did lots of taxying practice, and then some short hops just above the grass runway.
Then it was time to take-off. The Shadow climbed surprisingly steeply at 50kt, as I tried to keep it below the ‘flap’ speed. Landing is easier than I expected.
I did 5 flights in just over 24 hours, so I was stoked. After lots of circuits, I’m learning to control my speed on approach.
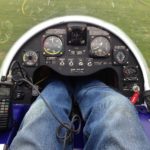
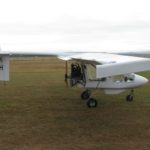
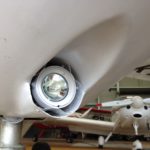
A new spring on the elevator trim tab, means that the Shadow will now climb ‘hands-free’ at 60kt airspeed, and it can be trimmed to fly straight and level by itself. It still needs further fine-tuning, hopefully getting it to hold a 50kt approach speed.
At the end of the second day, Murray suggested that I go for a “tiki tour” of the district. I headed south-west past the little town of Manapouri, then followed the Waiau River down to the diversion weir. A left turn took me up the Mararoa River for a few km, then I headed back west. It wasn’t long before I was calling “Kilo Lima Hotel joining right base for Runway 32”. Very satisfying feeling to have re-built and now flown this aircraft.